Energy saving becomes a more and more important topic in the industry. Since many decades the screw pumps have been used as a material feeding system, but now new developments regarding the wear resistance surface of rotary valves Coperion enable the successful substitution of screw pumps in existing lines with extreme energy savings.
A screw pump works with the principle of bulk material compaction in a screw barrel to seal the upstream product feeding from the conveying air. High rotational speed (1500 rpm) is necessary for the compaction of the bulk material by the screw barrel and the abrasiveness of the conveying product generates wear in the screw barrel and regular maintenance is necessary. Screw pumps have a high power requirement with motor sizes up to 300 kW while Coperion rotary valves motor are max 5 kW. In addition the screw pump has an average pressure drop of around 300 mbar, which increases the energy consumption on the air supply equipment.
Case study -lignite conveying (Location: Germany)
At plant in Germany, the customer installed a new silo and conveying system for lignite. The feeding capacity is max. 6.000 [kg/h] at a conveying pressure of 0,5 [bar] (7 PSI). In order to implement an explosion barrier between the conveying system and the silo, the customer chose a Coperion rotary valve ZXD 300 with DuroProtect® 3. This rotary valve accomplishes two functions: feeding airlock for the conveying line and explosion barrier (protection system).
The capital expenditure for this single conveying rotary valve solution was lower than the cost for overhauling the existing screw pump and also lower than the CAPEX for an explosion protection rotary valve required upstream of the screw pump. In addition, customer has achieved energy savings of more than 90% compared to the screw pump concept.
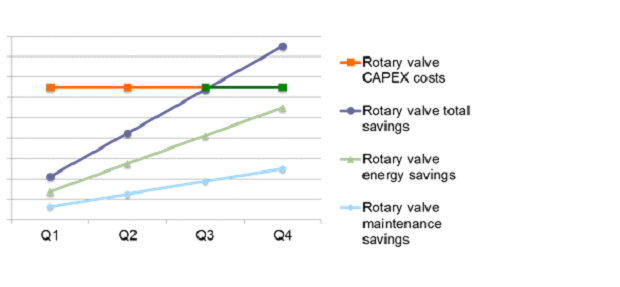
Payback graph of a screw pump replacement.